There is a lack of trust in remote audits from some in the food industry, according to an expert who looked into the subject for the Global Food Safety Initiative (GFSI).
Solely remote audits are not GFSI recognized but a blended audit, which involves virtual and onsite checks, is accepted. Certification program owners such as BRCGS and FSSC22000 are offering fully remote food safety audits.
Alan Gillies, managing director of AGLC, helped produce a report for the GFSI on remote audits but this has not yet been made public.
“GFSI started us off with a simple question: Is there valid science evidence out there to show we can deliver the same level of assurance by a video facilitated remote audit as by a site visit? The simple answer is no,” he said at the 2021 virtual GFSI Conference.
“We did find, because of what’s happened and industry response, there was a lot going on so another conclusion to GFSI was it was a real opportunity as an industry to learn from the year we’ve had, from what they have done in response to the pandemic and use that going forward. The other theme was video facilitated remote audits are the start of the journey of the use of technology in food safety. The goal of introducing technology should be to make auditors better and food safer. I don’t see the two in competition.”
Gillies, also chair of a GFSI panel on the use of ICT in remote audits, said not all the industry trusts the remote audit process.
“A number of people said they want to get back to doing audits properly which suggests people see this as a stopgap and those trying remote audits were generally doing it with their low risk sites. There was a lack of belief in some responses that we could get to the same level of trust,” he said.
Continuous monitoring instead of snapshot
Monitoring technologies are coming that allow the generation of a lot of data as you go instead of a snapshot model, which is part of traditional auditing, according to Gillies.
“Some people have said are we going to replace auditing with continuous monitoring? I don’t believe that is the case. We change the way people work but we don’t get rid of it altogether. If you move from a snapshot auditing system to one that is based on continuous monitoring then that can give us a lot of trust so we can see what is happening all the time and not just between audits. But then there is a need to verify the monitoring is finding what you think it’s finding and are the processes reliable. I think we will be changing the nature and relationships between the different types of audits but auditing is here to stay.”
Gillies said the future may be auditing the monitoring process rather than the food safety.
“We’ll need to audit that people understand what the data is telling them, that the equipment is working correctly and generating the right numbers and that we’re measuring what is important and not what is easy as they are not always the things safety relies on. I don’t think people need to worry about their jobs anytime soon. They need to be prepared for auditing to be disrupted but they’ll find new challenges in the technology facilitated world,” Gillies said.
Monitoring technologies are good at looking for problems you know are there, said Gillies.
“So if you predict these are the likely events it’s often easier to create monitoring systems to look for those continuously and find them.,” he said. “We can give the novel problems to the human beings. In any situation where you go in and are designing new ways of monitoring, the people who know best what the issues are, are those on the ground. The staff understand their process and environment.”
Feeding 22 million a day
Another session covered resiliency and technology with speakers from Nestlé, Cargill and Ecolab.
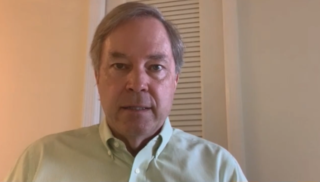
David Maclennan, CEO of Cargill, said there was a lot of pressure from state, local, federal and non-U.S. governments to continue making food to keep people fed.
“The key to a resilient food supply chain system is open access for trade, reducing barriers that are put up in panic moments like COVID by governments but we’ve got to keep food moving across borders.”
Maclennan added one of firm’s beef plants feeds 22 million people per day.
“The mantra is disrupt yourself or someone else is going to disrupt you. That being said, agriculture has been a little slower as an industry to adopt technology but the pace of change is increasing rapidly. People want to know more about where does their food come from. It’s no longer good enough to trust a brand, it’s who are their suppliers, what are those companies like? So the demand for knowledge and traceability on basic food consumption is higher than it’s ever been and it’s an area we’ve spent a significant amount of time developing technology.”
Disruption relative to COVID-19 meant business was not as usual, said Maclennan.
“We had one training session with 300,000 dairy farmers in China online,” he said. “There would have been no way to train them all at the same moment, other than through technology. Another example is artificial intelligence, we have facial recognition technology for cows. So it is able to track the dairy cows to see are they eating properly, are they getting enough water, what is their health and does the farmer need to change their feed rations or formulations as a cow isn’t drinking or eating properly.”
Solving issues faster
Natasa Matysova, head of quality management at Nestlé, said 2020 accelerated adoption of digital technologies.
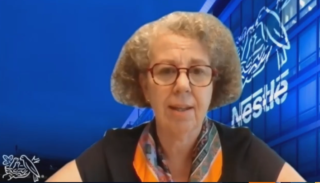
“It is the normal daily routine where you are monitoring your environment and sometimes having findings which you need to eradicate by proper cleaning and disinfection practices,” she said.
“So how do we empower our workers and those on the frontline to know the results? We use a connected worker platform which is a tablet enabled operation where the operator would see all the data he needs to run his line, whether it’s performance, quality checks or environmental monitoring results. He sees where the latest finding was, finds out what is the proper procedure and applies it. So the quality professional can refocus on making preventive actions, coaching and helping.”
Matysova said when a microorganism is found they use bioinformatics and whole genome sequencing to find out more.
“We can do this for Listeria and Salmonella and it tells us if the microorganism is a home-based bacteria or a visitor to the facility and we have to find the source in a raw material or people. When we have these events and need to support the factory because they may not have the expertise, in past years we would have flown people in and delayed the solution of the problem. Today we use Google Glass, we feel we are at the plant, we see the problem and help solve it at the site without delay,” she said.
“Whatever we have learned during this pandemic, it will stay and become routine practice. We have other digital tools helping us with predicting what come next, whether it is advanced analytics or artificial intelligence, it becomes a normal routine of working where we rely on data and make ourselves better to predict and eradicate before it has become a problem.”
Learning from incidents
Christophe Beck, CEO of Ecolab, spoke about three capabilities: predicting disruptions that could happen, helping customers respond and providing real time control to learn and prepare for the next problem.
“It can be African Swine Fever or an E. coli outbreak in a plant or a group of plants. Our customers and ourselves can see when things are going wrong, we know where the weakest link can be in a plant and help respond to that as quickly as we can. Every time there is a disruption we learn a bit more and become better at it.”
Beck said it would have been harder for industry to have managed operations 10 or 15 years ago.
“Since we have 40,000 systems around the world that are connected to the cloud, it helps us generate so many insights that we can compare across plants, companies or industries to understand what best and what worst looks like. We have 24/7 monitoring with customers connected to the cloud. We can address it remotely, prevent it and continue operations,” he said.
“We are seeing consumers shift from assuming it is trustworthy to you need to demonstrate to me that I should trust you. We’ve learned the hard way during the pandemic with our hotel and restaurant customers where many guests didn’t want to go to restaurants and hotels because they were worried they would get sick with COVID-19.”
(To sign up for a free subscription to Food Safety News, click here.)