you spin me right round —
Born for but never raced in F1, the idea found some success at Le Mans.
Eric Tegler
–
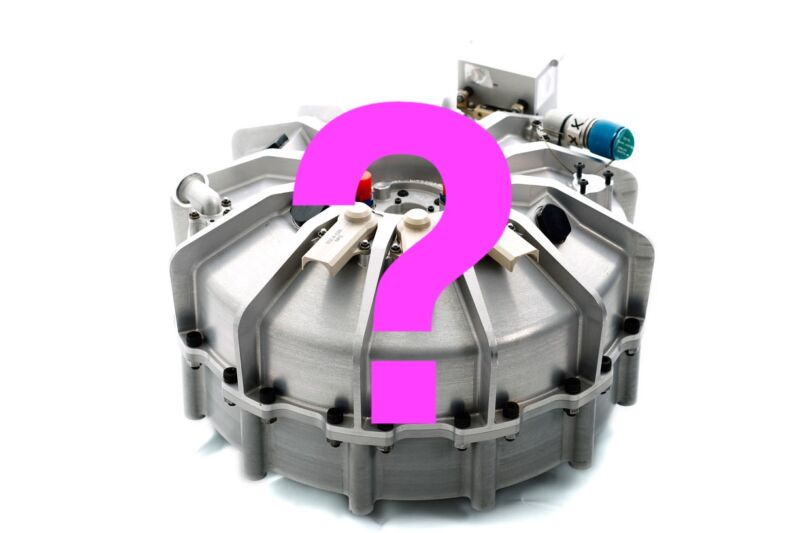
Enlarge / Why did the flywheel hybrid never catch on for road cars?
When a Speed network television crew interviewed Margo T. Oge, then-director of the Environmental Protection Agency’s Office of Transportation and Air Quality, during the 10-hour-long 2010 Petit Le Mans Series race at Road Atlanta, Porsche’s experimental 911 GT3 R Hybrid race car held down a top-20 position in the 45-car field.
The broadcast crew took every opportunity to call attention to the presence of the new Porsche. Hybrid street cars were becoming mainstream, and “road relevance” was repeatedly cited by Oge along with energy independence and low carbon emissions as EPA imperatives.
But, like its similarly new Formula One hybrid race car cousins, this special 911 GT3 R was not a street-going hybrid. This was a “flywheel hybrid.” Instead of parallel gasoline engine/electric motor drive systems combined with a battery, the 911 racer paired an internal combustion flat-six cylinder with an electro-mechanical flywheel energy storage system.
Porsche motorsports engineers began researching hybrid systems for racing in 2007. Around the same time, F1 decided to integrate hybrid tech. Starting with the 2009 season, F1 allowed its teams to use mild hybrid systems called kinetic energy recovery systems (KERS).
Most F1 teams developed KERS that used batteries, but the Williams F1 team created an electromechanical flywheel system. Williams ultimately did not race that system owing to Formula One technical regulations. (Interestingly, Chrysler attempted to build a natural gas/flywheel hybrid race car for Le Mans 15 years earlier, but that program never made it to a race either.)
In 2009, F1 teams were allowed to use hybrid systems for the first time. The Williams F1 team chose to develop one that used a flywheel instead of a chemical battery or capacitor as its energy store. However, the system never raced in F1.
This is what the Williams Hybrid Power flywheel looked like.
Williams set up a spin-off company, Williams Hybrid Power, to develop and refine the flywheel hybrid. In 2010, it partnered with Porsche Motorsport to build the 911 GT3 R Hybrid.
Audi then used the flywheel hybrid system to good effect in its R18 e-tron Quattro. This car would win Le Mans three times in a row.
An illustration of the Audi R18 e-tron Quattro hybrid system.
However, Porsche eventually licensed the concept from Williams Hybrid Power and set about adapting it to endurance racing in the 911 GT3 R Hybrid. Audi, too, had a go with a flywheel in its all-conquering R18 e-tron Quattro diesel-electric prototype. The Audi prototype used a system further developed by UK automotive/aerospace supplier, GKN, which acquired Williams Hybrid Power in 2014. This flywheel hybrid racer won dozens of races, including the 24 Hours of Le Mans, outright, in 2012, 2013, and 2014.
Given these high-profile racing factory programs nestled in F1 and sports car racing, many if not most casual observers expected flywheel hybrid technology to migrate to production vehicles within a few years.
That never happened. How come?
A high-RPM booster
In simple terms, an automotive flywheel hybrid system leverages power from a mechanical flywheel motor to augment power from an internal combustion engine for short periods. Electric motor/generators located at a vehicle’s wheels or axles produce electricity harvested from the kinetic energy, which is otherwise wasted as heat when friction brakes decelerate the vehicle.
But instead of sending the energy to a chemical battery for storage and redeployment, the electricity is used to drive a flywheel motor. Electrical energy is transferred to rotating kinetic energy by a novel magnetic material (sometimes a magnetic powder) embedded within the flywheel. The more energy applied, the faster it spins. (NB: this is different to the mechanical flywheel hybrid system that Nissan attempted unsuccessfully to develop for its 2015 Le Mans racer.)
The mass of the flywheel and the velocity at which it spins—typically from 25,000rpm up to 55,000rpm or more—determine the availability of energy it can release. To transfer the kinetic energy stored in the flywheel back into electrical energy, the rotating magnetic field generates a current in the reverse direction (by inverting the polarity of the applied voltage), and power is delivered to the same motor/generators that harvested energy during the original braking event.
As noted, the motor generators may be located at the wheels. Alternately, a flywheel motor may be connected to the engine driveshaft via a continuously variable transmission (CVT) or other coupler. When called for, it couples with the driveshaft, taking the potential energy from the flywheel and translating it to kinetic energy propelling the driveshaft and drive wheels.
Flywheel motors have often been compared to capacitors, capable of quickly storing and releasing energy. Proponents cite weight, cost, and environmental advantages over traditional chemical-battery hybrids.
The GT3 R Hybrid was built to compete in 2010’s running of the Nurburgring 24, a round-the-clock endurance race held at the famous track.
A top-down illustration of the GT3 R Hybrid’s powertrain. The components in red are the flywheel hybrid system, power electronics, and the two electric motor/generator units.
Another look at the GT3 R Hybrid’s powertrain.
In a road car, this would be the front passenger seat. In the GT3 R Hybrid, it was reserved for the flywheel.
In the 911 GT3 R, the flywheel motor used a carbon-fiber composite flywheel with a 16-inch (406mm) diameter. Mounted in a carbon fiber box where the passenger seat would be in a road-going 911, the flywheel motor received power from, and sent power to, an 80hp (60kW) electric motor/generator at each front wheel. The configuration allowed Porsche to incorporate torque vectoring to improve handling/traction when accelerating from corner apex out.
The flywheel motor in Porsche’s racer had a capacity of 0.2kWh. It could deliver 163hp (122kW) for up to six seconds, offering boost for acceleration—out of corners or for passing, depending on how/when the driver decided to apply the extra power via a steering wheel-mounted button.
The car had a total system output of about 670hp (500kW) and weighed approximately 2,866lbs (1,300kg). The flywheel and support structure reportedly weighed around 103lbs (47kg), considerably lighter than a battery-electric hybrid setup. In all, the car weighed 230lbs (104kg) more than the conventional Porsche GT3 cars it shared the track with.
Porsche viewed flywheel storage as more durable than lithium-ion batteries in the extreme power charge/discharge cycles of racing. Unlike a battery, the flywheel motor was capable of being fully charged (accelerated to its maximum speed) and discharged (decelerated to a near stop) multiple times a minute without adverse effects.
Thanks to its relative fuel efficiency—if not outright speed—the 911 GT3 R Hybrid actually led the 2010 Nürburgring 24 Hour race for eight hours before dropping out. At the 2010 Petit Le Mans, the car ultimately finished 18th, though attrition helped.
It raced again in 2011 but was put aside thereafter as Porsche concentrated on its 919 Hybrid World Endurance Championship prototype racer.
Slow, not fast, energy recovery & storage
The shift in Porsche’s racing commitment to the Le Mans-bound 919 Hybrid was partly connected to its contemporary road-going supercar project, according to Daniel Armbruster, president and CEO of Porsche Motorsport North America.
“It was around that time that work was also already underway on the 918 Spyder plug-in hybrid super sports car,” he remembers. “In both instances [919/918], it was found that lithium-ion batteries offered the best balance of energy retention and power delivery for their respective purposes.”
Despite its routine stop-start nature—and thus opportunities to harvest regenerative braking energy—street driving is not characterized by the need to sprint from corner apex to corner apex, braking and accelerating at maximum possible rates as in racing. The demand for quick, intensive energy recovery and subsequent deployment is replaced by a mandate for slower-paced electrical energy generation and deployment, shifting the emphasis to energy storage.
“The flywheel hybrid technology in the 911 GT3 R Hybrid offered fuel savings and therefore a reduced need for pit time versus the cars it competed against,” Armbruster explains. “In racing applications, it’s possible to make more effective use of a flywheel because of the frequent hard braking and acceleration that are both good matches for the short-term energy storage ability and high output capacity of that technology.
“But the technology wasn’t without challenges. In general, the flywheel does not store much energy, just the braking energy,” he says. “A battery is able to achieve highly stable long-term energy storage in a way that a flywheel simply cannot match. For road uses where the ability to drive on demand without local emissions is important, as is becoming increasingly the case in parts of Europe, a battery-based solution is the best hybrid powertrain option.”
While the limited storage capacity of the flywheel hybrid sidelined the technology for Porsche, Armbruster adds that “there is no denying that the 911 GT3 R Hybrid played a pivotal role in proving that hybrid technology had a home in high-performance sports car applications.”
Looking back to that time from the present day, Glen Pascoe, principal design engineer with Williams Advanced Engineering (WAE), says that the quick capture and release of energy by flywheel motor systems is better suited to peak cycle applications.
“Besides city-center use, the duty cycle for a typical passenger car does not suit the repeated ‘start-stop’ nature that best suits flywheel technology,” says Pascoe. “The stored energy in a flywheel is always depleting, unlike a chemical battery, which can hold its state of charge over a very long period of time.”
On the buses
Williams’ basic flywheel hybrid concept did reach city centers in 2015 when GKN modified the system for London buses. GKN’s Gyrodrive flywheel hybrid system included a traction motor driven from the vehicle’s drive axle, an electric flywheel, an inverter for the motor/flywheel unit, and an electronic control system.
The system, and subsequent variations, have seen use in buses from UK manufacturer Alexander Dennis in both single and double-decker bus models. However, the Gyrodrive flywheel system was considered too large and expensive for urban-use cars (taxis), which adopted various battery strategies.
Glen Pascoe says WAE is not specifically refining any flywheel systems at the present but adds that “as we work across a wide range of industries and examine the requirements of our clients in detail, this technology may be appropriate for certain applications in the future.”
That could include racing if racing series/sanctioning bodies allowed such devices, though current interest appears to lie more in hybrid battery and fast-charging development. WAE is currently engaged in hydrogen fuel cell development for large mining trucks, using regenerative braking in much the same way as with flywheel systems.
Porsche Motorsport North America’s president says the company “is always evaluating which technologies offer the best solution for the current situation,” not ruling out any single approach.
Armbruster explains that Porsche’s strategy “includes internal combustion powertrains, sporty plug-in hybrids and fully electric vehicles… We are also investigating the development of synthetic fuels that offer an environmentally sound approach to internal combustion vehicles that are already on the road.”
Ironically, the flywheel hybrids that most of us now encounter lie in vehicles we ride in (buses, trains, ships) rather than drive. And static flywheel systems are also under development; in Germany, a company called Chakratec has just installed a flywheel storage system at a Premier Inn in Leipzig, designed to manage peak loads for EV chargers.
But about a decade ago flywheel-motor-augmented race cars led the Nürburgring 24 and competed credibly against lighter GT3 cars. Further investment could both lighten and potentially improve the energy storage capacity of such systems, again pairing drivers and flywheels in a sport that rarely throws everything away.